FROM MAGAZINE: Warehousing is redrawing the logistics network in Africa
Modern warehousing in Africa, coupled with its security measures, is shyly on the rise and while it is a means to tight African supply chain, the lack of wide adoption remains a concern. However, with heavy investments pouring into logistics infrastructure and the awaited commencement of African Continental Free Trade
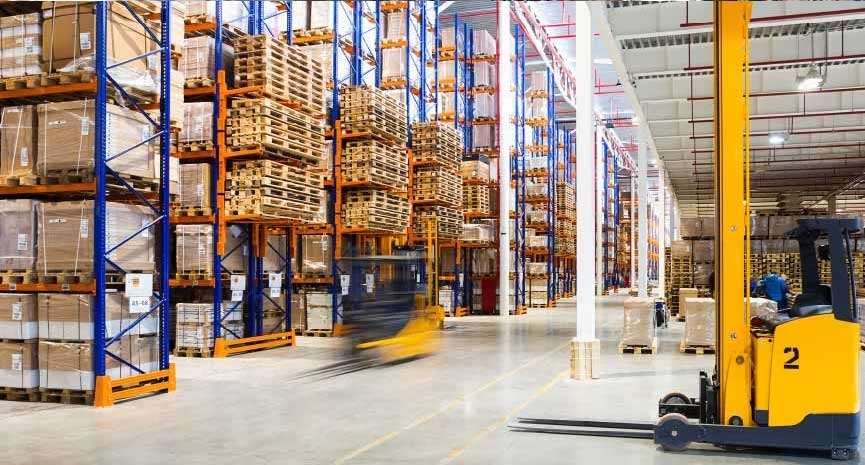
Modern warehousing in Africa, coupled with its security measures, is shyly on the rise and while it is a means to tight African supply chain, the lack of wide adoption remains a concern. However, with heavy investments pouring into logistics infrastructure and the awaited commencement of African Continental Free Trade Area (AfCFTA) agreement, warehousing sector in Africa is in the midst of its transformation.
In Africa, warehousing strategies and facilities have remained the same for decades. And the sector tends to be the most ignored link in the supply chain. Now, with imports and exports compromised due to escalating Covid-19 cases, which have been reported in 23 countries in Africa at the time of writing this story, and the prospect of freeing the African continental area for trade, large scale modern warehouses are likely to proliferate and facilitate local manufacturing. Moreover, the already booming ecommerce sphere and the popular choice of outsourcing logistics services are thriving to bring the needed international grade warehousing facilities to the region. Boosting the overall economy, Industrial real estate demand is estimated at over 15 million m² in Africa’s highest-potential markets.
Africa’s exponentially growing ecommerce industry and the rapid adoption of third party logistics (3PL) services are driving the demand for speculative warehouses. These warehouses can conveniently be divided into small units and accommodate multiple tenets and are flexible to meet many requirements of different goods dealt by ecommerce businesses and 3PL services.
The AfCFTA agreement is expected to take an economic turn historically seen during the formation of World Trade Organisation (WTO). The agreement, which is scheduled for 1st of July, 2020, will enfold a market of more than 1.2 billion people with a combined gross domestic product (GDP) of more than USD 3.4 trillion. The trade-marriage between 55 member states of the African Union has the potential to increase the trade by a spectacular 52.3 percent, eliminating the import duties, as estimated by the United Nations Economic Commission for Africa (UNECA). Also, according to the Ken Research, logistics and warehousing market is expected to reach USD 80 billion by 2023.
William Ojonyo, who is the national chairman of Kenya international freight and warehousing association (KIFWA), commented that “Warehousing will certainly be the distribution option after the commencement of AfCFTA, with a bigger market and bigger consumer base. Africa will have to embrace strategic commodity warehousing since the commencement will mean more intra-Africa trade with controlled external tariff, transportation challenges and inter-connectivity by air, road and rail. The continent will be left to rely on the corridors to enhance the goods and services trade which can only encourage block warehousing anchored on the major corridors”
Containing the challenges
One of the major complaints of international community and local businesses concerning African logistics is the poor infrastructure that serves as the weakest link in supply chain, dragging the overall speed of the shipment implicitly down. Logistics surrounding humanitarian services in Africa provides a revealing case.
In an attempt to circumvent the poor infrastructure, historically, the International humanitarian and other peacekeeping operations, which are very vibrant in the region, supported the use of ad hoc and contingency-scheduled missions. However, the increased support demands, poor specialised storage facilities and inefficient distribution hubs are further turning the system immoderately unreliable. Currently, continuing the humanitarian services in face of Lassa virus and coronavirus epidemics, a hub-and-spoke distribution network is put in place, with main hubs on the West African coast.
Quality constraints in port infrastructure, as reported by the African Development Bank (AfDB), like limited capacity in terminal storage, operation, and maintenance severely limit the scope of logistics in the region. The bank has also estimated that an investment of USD 130-170 billion per year is needed to tackle the continent’s lack of quality roads, warehouses, power and other infrastructure. Apart from the storage constraints and inefficient distribution hubs, shortcomings like lack of real-time accuracy and visibility of available stock levels and manual interventions breed inaccuracies and affect stock valuation. Adding more to the problem, manual stock retrieval and racking further heightens the worry of goods not being correctly stored.
Having put forth the challenges and shortcomings, a few logistics corporations like Africa Logistics Properties (ALP), Agility Africa etc. are strategically setting up warehouses in key locations —ports and junctions— across the region that are eliminating the complications of buying land for entrepreneurs and small and medium enterprises (SMEs), giving access to fully secure, affordable modern warehousing facilities. ALP develops and manages modern grade-A warehousing across Sub-Saharan Africa and Agility has logistics parks in Cote D’Ivoire, Mozambique, Ghana and Nigeria. The adoption of modern warehousing is essential in bringing down the overall logistics cost going ahead.
Containing the challenges, the companies mentioned above have set up class-A warehouses across the region. These warehouses are typically high with around twelve meters height, enabling high stacking of the goods. This enhances the storage density, driving down the storage cost significantly. The warehouses are also equipped with moderate automation and digital infrastructure, which includes mechanical handling equipment, utility vehicles and warehouse management system.
Strategic warehousing near ports and railways
Africa is perpetually erupting infrastructure to facilitate trade. For example, the LAPSSET project –Lamu port, South Sudan, Ethiopia transport corridor, which is Eastern Africa’s largest infrastructure project bringing together Kenya, Ethiopia and South Sudan; Lagos-Calabar Coastal railway in Nigeria; Mombasa-Nairobi Standard Gauge Railway (SGR) in Kenya etc. are potentially shifting the course of warehousing, bringing in new challenges and regulations. Let’s explore the regulatory and economic challenges at the SGR route, which recently saw (and continues to see) protests drawn due to increased cargo transportation cost inducted by the new government regulation.
SGR route connects Mombasa port to capital city, Nairobi, along with intermediary towns: Mariakani, Miasenyi, Voi, Mtito Andei, Kibwezi, Emali, Athi River. In 2019, the government passed a policy forcing all cargo being cleared in the port of Mombasa and railed to Nairobi, an immoderate directive which cargo traders protested.
William Ojonyo, who is also the managing director of Peleceer Group, which is well placed in forwarding, clearing and warehousing businesses, sharing his insights on viable options for warehousing considering the new development suggested that “The consequent directive that all cargo must be railed to Nairobi created challenges that needed quick fixes to reduce the high costs, which in an essence meant that all cargo must be cleared out of the port in 4 days if the traders are to avoid port storage. The effect further meant that it is incumbent on the trader to find alternative storage facility on bulk cargo for further distribution to wholesalers and or consumers.”
The viable option: “The only viable option is strategic warehousing after port clearance, especially after the introduction of further surcharge of $200 and $100 for FEU and TEU respectively immediately after customs release, which has made keeping the boxes a day longer at the port facility after customs release extremely expensive.”
Facilitating manufacturing
To encourage manufacturing initiatives, it is crucial for warehousing sector to pave the way to grow the manufacturing output of the region, especially for pharma sector, as the African continent relies significantly on India for pharma products. Speaking on how the collaboration of manufacturing and warehousing is expected to look like, Ojonyo opined that “Rise in pharma manufacturing sector becomes a more critical consumer centric end product that needs controlled distribution across the country (Kenya) and the African region at large, most manufacturing companies find it cost effective to maintain their core business of manufacturing and leave the warehousing and subsequent distribution to the strategic market who have the option of mapping out demand and subsequent distribution.”
Underscoring the sustenance of cost effective environment for the manufacturing sector, logistics operations need to be equally economic, and a trend of moving warehousing facilities away from cost intensive cities to more sustainable locations is being sought out.
Sharing a possible case of Kenya’s future warehousing, Ojonyo highlighted that “Warehousing will continue to depend on the implementation of the Trade Facilitation Agreement (TFA), the process of clearance and cargo handling should equally be decentralised effectively from Mombasa and Nairobi if meaningful trade distribution will be part of the transition. For now it remains policy on paper, yet to be tested by the traders as a better option. Most significant would be the operational areas determined by the SGR cargo terminus, which would dictate strategic warehousing for businesses. I see main warehousing attraction in three major towns: Mombasa as the port of entry, Nairobi as the main city through which part of the SGR first leg terminates and Kisumu which has both potential for airfreight, water transport and rail transport to service the regions and the western part of Kenya. It is just a matter of time for warehousing to become the most preferred service after manufacturing and or bulk finished cargo imports.”
The new large-scale, modern warehouse parks are facilitating logistics and manufacturing clusters across Africa and creating an interconnected network, enabling more intra-regional trade. Currently, intra-regional trade accounts for just 17 percent of Africa’s exports, compared to 59 percent in Asia and 69 percent in Europe.
What is creating the waves?
Africa’s high interests in trade infrastructure; and growing ecommerce and 3PL are inevitably pushing warehousing sector to form an efficient network, which will inevitably reduce the overall cost of logistics in Africa and significantly reduce the supply chain time. The retail sector is adding momentum to the warehousing sphere, too. More than 70 percent of the world’s largest consumer goods companies are already operating in Africa, and there are a number of high-profile companies influencing institutional changes in the region. A study conducted by the Ichikowitz Family Foundation charity showed that around half of the young participants across Africa said that if offered USD 100, they would want to start a business. Of that, nearly 17 percent showed interest in investing in retail business. This is the kind of entrepreneurial wave African warehousing sector has to contain going ahead.
This feature was originally published in March - April 2020 issue of Logistics Update Africa.