Africa's Cold Chain Market setting remarkable trends
By 2050, Africa is expected to exceed the population of China and India, with 60% of Africa’s population being urbanised by 2050 and the number of middle-class households rapidly increasing.
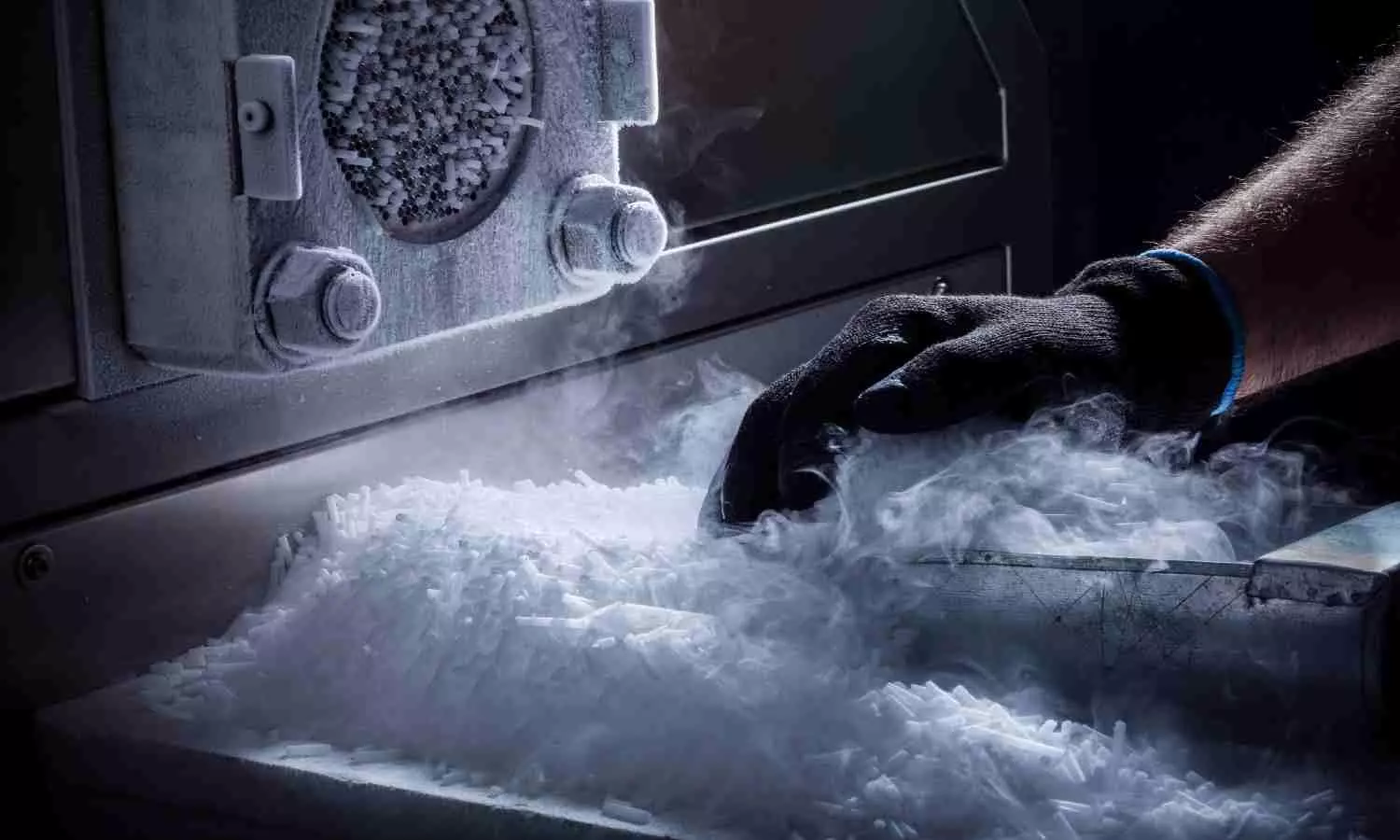
In recent years, Africa has seen a significant increase in the demand for effective cold chain packaging solutions. The continent's rising economy and the growing need of protecting the quality and safety of temperature-sensitive items all contribute to this increase in interest.
The rising need for temperature-controlled items in the continent, the entry of many new businesses, and government efforts and programmes are projected to boost the cold chain industry. The South African government has launched the National Transport Master Plan 2050 to oversee the construction of a multimodal transport system to fulfil the country's long-term transport demands.
Changes in lifestyle and urbanisation contributed to increased domestic consumption of processed foods and a shift in consumption patterns as people became more health concerned after Covid-19, thus assisting the market's growth. Because most industrial districts are located nearby, major cities such as Gauteng, Cape Town, and Durban are emerging as hotspots for the cold chain industry.
African governments are embracing the challenges of maintaining a continuous cold chain, assuring the delivery of perishable foods from farm to fork through innovative technologies and strategic collaborations.
Promising Trends
The utilisation of innovative technology is a trend that is gaining pace in the African cold chain packaging business. Smart packaging solutions, which employ sensors to monitor temperature, humidity, and other environmental factors during shipping and storage, are increasingly being invested in by businesses. These technologies are expected to play an important role in ensuring that items arrive in optimal condition.
“The use of real time temperature recorders within packaging is the most recent trend. Exporters can track and trace their products and determine if there were any delays or temperature excursions that will hamper product quality. These temperature monitors use cellular towers to transmit the information. Decisions relating to the product can then be made by the exporters. Some of these decisions include reducing waste and loss as well as determining the shelf life of the product,” said Vijan Chetty, Board of Director, Cold Chain Association.
“The use of real time temperature recorders within packaging is the most recent trend. Exporters can track and trace their products and determine if there were any delays or temperature excursions that will hamper product quality.”
Vijan Chetty, Board of Director, Cold Chain Association
Covid-19 unveiled the continent’s risk-prone reliance on foreign sources of pharmaceutical products. However, since then, leading pharmaceutical manufacturers, such as Moderna and BioNtech, have invested in building facilities in Africa.
“This shifting trend towards producing pharmaceutical goods within Africa aligns also with the African Union and African Centres for Disease Control and Prevention’s goal to produce 60% of Africa’s vaccine needs locally by 2040. With this sudden influx of domestic manufacture, cold chains will continue to be pushed to globalise. Improving both the proximity and availability of Tower containers is the safest way to meet these needs, so investing in our hub network remains a core focus for our business strategy. With an optimised global network for localised delivery, this enables us to react even more quickly to customer requests,” said Nosipho Ntshangase, Business Development Manager – Africa, Tower Cold Chain Solutions.
What the Consumer Wants?
Africa's rapidly growing population and expanding consumer markets have boosted the need for dependable and efficient cold chain packaging solutions. As the continent's economies expand, businesses such as agribusiness, medicines, and food processing strive to suit the changing requirements of African customers while guaranteeing the safety and quality of their goods.
“Consumers want products that are environmentally friendly and fresh with longer shelf life and a reduction in food loss and waste. Within South Africa the air cargo handlers are constantly reviewing concepts to improve on the integrity of the product. The combination of cool packaging material example gel packs, thermal blankets and dry ice is the latest trend within South Africa. This is due to the geographical position of South Africa to its consumers and to reduce food loss and waste,” said Chetty.
“With a growing prominence for personalised medicines, we are now beginning to see the advancements of precision therapies in the pharmaceutical industry. There is no longer a ‘one-size-fits-all’ approach to medical intervention. Instead, we’re seeing a move towards bio-specific treatments, tailored to a particular individual’s needs based on their genome. In response to consumer demand, Tower recently developed the KTEvolution, a container which can easily be carried by 1 or 2 people. Available in 26-litre and 57-litre options, the KTEvolution is available across Tower’s full temperature range and is ideal for the rising trend in smaller shipments such as direct-to-patient, samples shipment, and last-mile deliveries,” added Ntshangase.
Demand for efficient and sustainable cold-chain transport is increasing due to the growth in the biopharma market, which now requires more medicines that need temperature-controlled transport.
“Our Releye range of containers meets this demand with large, thermally-controlled units like the Releye RAP. To meet our customers’ demand for monitoring and autonomy, we also offer our Control Tower managed service as standard with the Releye range and plan to extend this service to all our other solutions. We’re also seeing growth in the market for personalised medicines and cell and gene therapies, which require specialist -70°C transportation. To meet this need, we offer our CryoSure solution. These dewars (vacuum flasks) can keep a constant temperature as low as -70° for up to three weeks and are perfect for products such as clinical trials, vaccines, diagnostics biospecimen and many more,” said Fredrik Linnér, Chief Business Development Officer, Envirotainer.
Need to Drive Technology
Technological advancements have significantly influenced the development and deployment of cold chain packaging solutions in Africa. These developments have resulted in the development of innovative packaging materials, technologies, and tactics that have enhanced the quality and safety of perishable items, decreased product waste and spoilage, and boosted supply chain efficiency. However, there are several challenges that market participants are confronting and considering solutions for.
“The unique set of challenges within the supply chain within Africa necessitates innovation and technology for cold chain packaging. Some of the products are required to reach the most rural regions that are not always accessible by road, rail or air. Therefore, especially within the continent of Africa there is a strong drive towards innovation and the use of technology as a solution to complex logistical challenges. The technological and innovation drive is to make the solution affordable and accessible to the continent,” said Chetty.
“The shifting trend towards producing pharmaceutical goods within Africa aligns also with the African Union and African Centres for Disease Control and Prevention’s goal to produce 60% of Africa’s vaccine needs locally by 2040. With this sudden influx of domestic manufacture, cold chains will continue to be pushed to globalise.”
Nosipho Ntshangase, Business Development Manager – Africa, Tower Cold Chain Solutions
Like all international pharmaceutical supply chains, cold chain operators in Africa must continually upgrade technology to ensure efficiency, integrity, and safety. Demand for increased visibility will drive businesses to innovate and add value to services.
“Cold chain logistics providers must invest in the latest on-board equipment built into our containers to track temperature and location, and to make data available to partners and customers. Smart packaging which delivers end-to-end traceability and precise shipment tracking is now a cornerstone of supply chain fulfilment in Africa. Built into all Tower containers are data loggers, designed to monitor external and internal temperatures throughout the container's journey. Assurance of physical and temperature product integrity is paramount in the cold chain which is why reliability is a key foundation for Tower. Data downloaded from over 20,000 shipments demonstrates fewer than 0.1% of temperature excursions on average, a vital indicator in the maintenance of the cold chain ,” said Ntshangase.
Infrastructure is also a Challenge
Animal and human specimens, vaccines, medications, and human blood are just a few of the commodities that must be packaged and transported with extreme care to ensure proper temperature and handling practices. This is mostly owing to the product's nature and the fact that these items are possibly dangerous. Given this, the final mile becomes a serious issue in Africa due to the lack of infrastructure, particularly in the continent's rural parts.
“The temperature requirements on air freight perishable produce can be maintained using cold chain packaging and material to reduce temperature loss. On some products the temperature solution used is often associated with the insulation properties of storage containers to maintain the integrity of the product quality. The escalating cost of logistics within the African continent often leads to the industry using the cheapest cold chain packaging solution that may not assist to maintain the temperature of products. The accessibility of the suitable cold chain packaging is also another stumbling block within rural regions within Africa. Hence cold chain packaging is not easily and widely accessible in all areas within Africa. In most cases the most available cold chain packaging is used that may not necessarily be the most suitable,” said Chetty.
“Paradoxically, despite a high demand for projects and sufficient capital, there is no rapid action in terms of infrastructure investment. With local distribution partners often having to deal with farm or rural deliveries where the patient or medical centre resides in isolated, remote areas, these deliveries are extremely challenging with containers requiring an electricity source, where infrastructure is not available to support a compliant supply chain. It is here however that passive temperature-controlled technology has helped simplify the delivery of thermally sensitive pharmaceutical items,” said Ntshangase.
Manufacturers demand not just optimal networking, but also guarantee of product integrity for patients, given the high value of pharmaceutical items, their perishable nature, and vulnerability to temperature variations. The selection of the most appropriate cold chain solution makes all the difference here.
“We are committed to constantly pushing the boundaries of what is possible in cold-chain containers. Our Releye range consists of giant, battery-powered, and insulated units that can hold up to five pallets of pharmaceuticals, depending on the size and model. These units are specifically designed to maintain a constant internal temperature for up to a week once fully charged and can deal with outside temperatures of up to +49°C. We are investing heavily in expanding our fleet of 7,500 FAA and EASA certified containers by an additional 1,300 in 2023. This will allow us to ensure that we are always able to meet the growing demand for cold storage solutions,” said Linnér.
“Tower’s critical and mission-defining objective is to improve the quality and consistency of pharmaceutical deliveries across a global market. We achieve this through innovative structural design of our passive containers, meaning pharmaceutical products stored and transported in a Tower container, require zero in-transit manual intervention,” Ntshangase added.
Logistical Challenges
In the world of logistics, each product has distinct qualities that necessitate particular handling and shipping procedures. The logistical challenges of transporting various items are enormous, necessitating careful preparation and execution to guarantee that they arrive in optimal condition.
“The staff at airport handling facilities must be trained on how to handle different products. The time temperature tolerances and handling of products differ. Staff are required to be trained on how to handle different products. A good example is citrus fruit has a greater tolerance for higher temperatures than table grapes. Table grapes cannot be left at ambient conditions for too long and deviations in optimum temperature regimes must be kept to a minimum. Airfreight shipments of citrus should be sent to the aircraft before table grapes. Staff understanding these handling conditions will assist to reduce food loss and waste and improve the shelf life of products,” said Chetty.
With the South African Health Products Regulatory Authority (SAHPRA) clamping down on a number of players, Good Distribution Practices (GDP) continues to be an important aspect of cold chain logistics. Temperature-controlled containers are an important part of this, but manufacturers may struggle to find the correct solution for certain shipments.
“We are investing heavily in expanding our fleet of 7,500 FAA and EASA certified containers by an additional 1,300 in 2023. This will allow us to ensure that we are always able to meet the growing demand for cold storage solutions.”
Fredrik Linnér, Chief Business Development Officer, Envirotainer
“Tower Cold Chain offers a comprehensive variety of sizes, volumes and temperatures, ranging from 3075 litres down to 26.4 litres. All solutions provide an industry standard 120+ hour protection for products that require an internal temperature of -80°C (ultracold), -60°C (ultracold), -20°C (frozen), +5°C (refrigerated) and +20°C (controlled room temperature). At Tower, we provide employees with up-to-date GDP training. As active pharmaceutical ingredients, clinical trials, small batch-shipments, and commercial medicinal products become more stringent on quality in recent years, awareness and education must be enforced to ensure compliance and quality standards are followed,” said Ntshangase.
“While our primary focus is on pharmaceuticals, we understand that different products require different types of handling, and this is something we take very seriously. Approximately 99 per cent of the cargo carried within our containers are of the pharma variety. To ensure that anyone who comes across our containers is trained to handle them properly, we provide comprehensive training programmes through our academy. These courses are designed to equip attendees with the knowledge and skills they need to ensure the safe delivery of pharmaceuticals and to meet the requirements of a more demanding regulatory landscape,” said Linnér.
The African cold chain packaging business is changing dramatically, with an emphasis on eco-friendly materials, sophisticated technology, reusable packaging, and blockchain. These changes are projected to benefit the industry by increasing the quality and safety of perishable goods while lowering the environmental effect of packaging solutions.
Technological advancements have been critical in the development and implementation of cold chain packaging solutions in Africa. As technology advances, the African cold chain packaging industry is expected to adopt new solutions that improve the overall sustainability and effectiveness of the supply chain.