'The Air Cargo Safety Center(ARC) will allow us to continue to innovate at a faster rate than we have before'
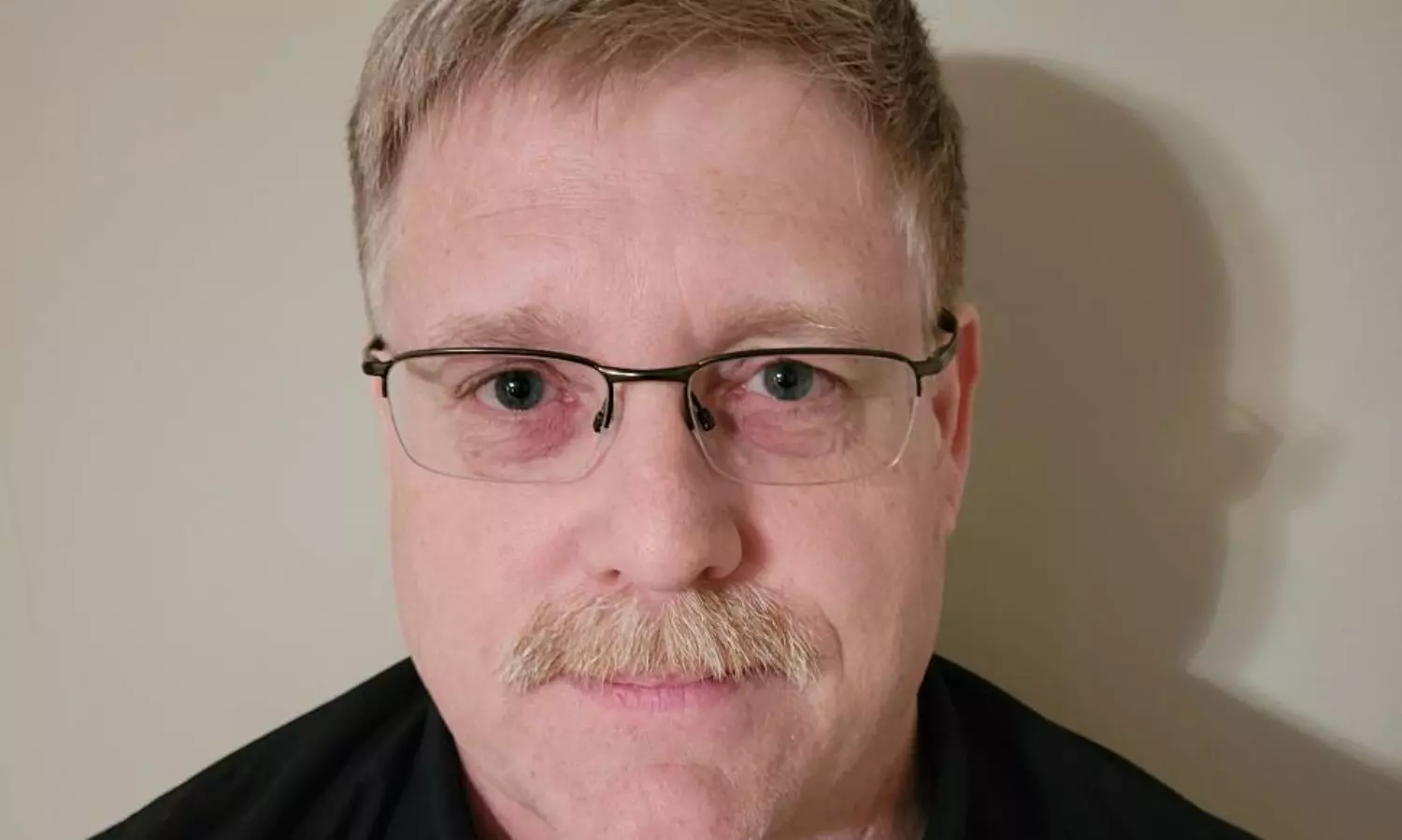
David Lee is Satco's SVP of Engineering & Innovations
Satco, Inc. recently made a $10 million investment culminating in the opening of the world's first manufacturer-owned Air Cargo Safety Research Center (ARC) in Miami Township, Ohio. The Satco ARC facility places an emphasis on optimizing the manufacturing process and safety of unit load devices (ULDs), ultimately increasing the safety of air cargo transportation. Lakshmi Ajay, Logistics Update Africa spoke with Satco's SVP of Engineering & Innovations, David Lee as part of our #SafetoFly campaign
What are some of the fundamentals of building some of the safest ULDs on the market and what are the roadblocks?
The aircraft and the ULDs they carry are the last line of defense when it comes to cargo fires. It starts with the shippers and proper identification of materials being shipped and those materials being properly packaged for shipment. Material options as well as design to limit the amount of airflow in/out of the ULD. This design process is key to controlling and containing the fire inside of the ULD to allow the flight crew to safely land the aircraft. The only roadblock if any is the cost of materials and what the ULD owners are willing to pay for the ULD as they conduct their own internal risk assessments.
Considering that the air cargo industry has had a revival in many countries owing to the pandemic, has there been a rise in demand for your products including the ULDs, pallets, and nets? Have there been any fluctuations in their prices?
The pandemic has "sped up" up the e-commerce piece of the shipping industry somewhat faster than expected, however, the last two years has also caused supply chain disruptions to what would be normal shipping patterns causing there to be an increase in demand for ULD products and at the same time, pressures on the supply chain. Due to the current inflationary pricing on raw materials and goods as well as increased labor costs, both issues have coupled with the supply chain delays, all of these factors have driven cost increases of ULD goods to our customers.
What can you tell us specifically about your product /unit load devices that can tackle fire hazards? What kind of components is being used to manufacture them? How do they work and what kind of industry reception have they had considering that fire hazards and shipment of Lithium and Lithium-ion batteries is a hot button issue with the aviation sector in general in recent times?
Our containers and pallet fire containment covers are designed to contain cargo fires for a minimum of 6 hours. There is currently no testing specification for class "D" fires or the classification that Lithium /Lithium-ion batteries fall into, however from our industry experience and working with our customers, we have set minimum specifications that we target to meet and test for with our ULD products. We are also working closely with the industry to develop those specifications as we move forward to standardized testing requirements to be followed by the Equipment Manufacturers, following the same process that established the requirements for standard class "A" fire load testing.
What are some of the objectives for the fire safety test facility or burn lab at Satco ARC?
The Air Cargo Safety Center(ARC) will allow us to continue to innovate at a faster rate than we have before. The facility that we have designed will allow us to have total control over the process that in the past has had us rely on third-party vendors to conduct tests. The research and development costs associated with these products are very expensive for our industry to undertake and now our investment will allow us to test concepts and materials at will. Our number one priority is people, it is about air cargo and flight safety. Our goal is to be able to offer our customers and the airline industry the safest ULD products available. Our Ohio facility gives our team the tools and resources they need to innovate and create these products.
The containers shown have all been successfully tested to contain a fire consisting of 5,000 Lithium-ion batteries with no flame penetration for a minimum of six hours. These are all in the product stage. They're in-service today, circulating around the globe helping airlines safely transport cargo
What kind of research and outcomes for the air cargo and aviation sector can we expect to come out of the Air Cargo Research and Safety facility ARC in Ohio? What has the industry reception to the ARC been like?
Our investment in our Ohio facility and the number one objective is people and safety; to help our customers and the airline industry have access to ULDs that are capable of containing cargo fires. ULDs are not the answer in avoiding cargo fires, however, they are an extremely important part in protecting the people and aircraft assets as a line of defense if a cargo fire were to happen onboard and in flight. Our public announcement about the Ohio facility is still fresh (March 11, 2022), however, we have received several hundred views to our posts and many requests for additional information on our products.
How old is the Satco Rental business? How much does the rentals business contribute to the overall revenues and has this been growing- post the pandemic or in the recent 3-4 years and if so to what do you attribute this growth to?
ULD Rentals is our newest business division, launched in September 2020. Our standard fleet of Class A fire-resistant containers are among the safest and differentiators in the industry. We continue to grow our fleet size and types of ULDs based on customer requests. We have a very large quantity of pallet/nets available for our rental customers as well as containers for all types of aircraft fleets, both upper and lower deck ULDs. We are uniquely positioned in the ULD Rental / Leasing market being the original equipment manufacturer (OEM) for ULDs of all types including the cargo nets and cargo straps.
As sustainability and green initiatives are a big part of the air cargo and aviation sector now, what are some ways in which Satco Inc has brought sustainable features to its products and offerings?
Our ULDs are made mostly from aircraft-grade aluminum and those materials are 100% recyclable once retired from service. Many of the composite materials that we use in our products have also found their way into recycling programs as well being used for or as additives to other fiber-based products as well. We have also been working to reduce tare weight of our products to help our customers reduce aircraft fuel burn and carbon emissions. Our company is also looking to other technologies in sustainability and green initiatives, but more on that program in the very near future.